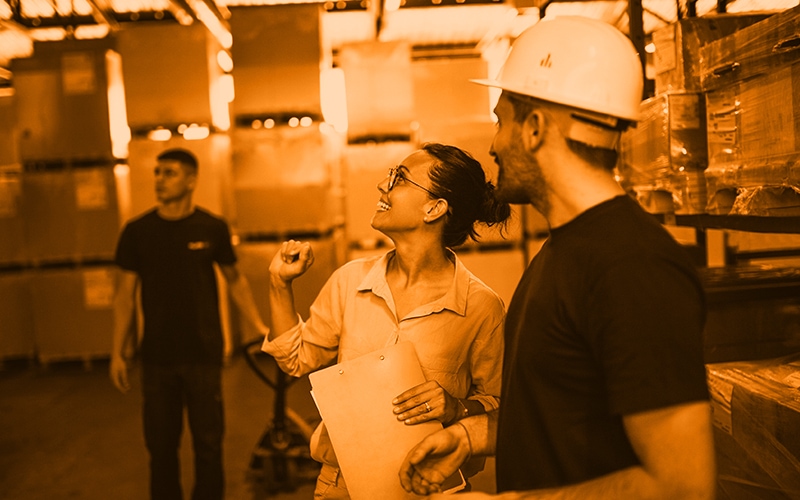
Using JobPack® to Schedule Maintenance and Reduce Downtime
Unplanned downtime costs manufacturers upwards of $50 billion a year. Here’s how you can break the run-to-fail cycle.
Manufacturers across the country are struggling with a common problem: unplanned downtime. Causes of unplanned downtime range from supply shortages to worker injury, but by far the most common instigator is equipment failure. This is because many manufacturers, reluctant to take their machines offline for maintenance, instead push their machines until they break. This run-to-fail mindset means that manufacturers are constantly scrambling to react to machine failure, rather than taking proactive steps to maintain their equipment—and it’s costing them a lot of money.
Ways unplanned downtime impacts the manufacturing bottom line:
- Operating expenses stay the same while production sits idle.
- Perishable product goes bad while waiting for the machine to come back online.
- Reduced capacity leaves manufacturers with less flexibility to take on new jobs.
- Backlogged work orders pile up and require overtime or outside contractors to finish.
- Repair costs are higher than maintenance costs.
Those are just the most obvious costs. Less tangible costs include increased stress on the workforce, lower job satisfaction, higher turnover, and damaged customer trust.
Given the pervasiveness of this problem, you might be forgiven for assuming there’s no workable solution. The good news, however, is that there are alternatives to the run-to-fail cycle, and they lie in preventative maintenance enabled by machine monitoring and production scheduling software. Here’s how you can apply these software insights to your manufacturing business.
Use machine monitoring to track usage and spot underperforming tools.
The first question manufacturers need to answer if they’re going to prevent unplanned downtime is “what does normal uptime for my factory look like?” Often times the perceived uptime is different from actual uptime. This is because manufacturers may not properly account for factors such as changeover or inspection time.
However, machine monitoring can also detect more troubling signs that a tool is not performing up to standard. If it’s taking longer to machine components on Lathe A than on Lathe B, it may be a sign that Lathe A requires maintenance. Making those repairs early can prevent a more serious breakdown later.
Plan for routine maintenance before equipment breaks down.
While maintenance downtime is usually shorter than repair downtime, it still represents a period of time when your tools are not delivering value. To be efficient with your repairs, it’s key to identify points in your manufacturing schedule where your machines will be either naturally offline, or where you can arrange workloads to allow for repairs to take place.
JobPack®’s scheduling tools make identifying these low-volume windows easy to spot. If you know how long the repairs are intended to take, you can move projects to other machines, or else make necessary adjustments in your production schedule early enough to free up the machine for repairs without impacting your on-time delivery rate.
Record past maintenance to ensure a regular schedule.
Even with the best intentions, businesses can fall behind on their maintenance schedule if they haven’t kept proper track of it. Given the number of different machines running in a factory at once, and their varying maintenance needs, keeping them all in working order is more complicated than a checkup now and then.
Instead, manufacturers need to track all the different maintenance tasks that each machine requires, how often each needs to take place, and what parts need to be on hand to keep them up and running. The last thing a manufacturer wants to discover is that a routine replacement part has not been kept in stock—especially if ordering one in may take a while. A maintenance schedule can include an inventory check so that new parts can be ordered in time if needed.
Gain visibility into how to respond to unplanned downtime.
If the worst does happen and your machines go offline, JobPack®’s scheduling tools can help you recover. Because JobPack®’s scheduler offers full oversight of all your production processes, any time a machine breaks down you can run an analysis to see how the cascading effects of that downtime will impact your other projects. You can then run “what if” scenarios to see how shifting projects around might help you minimize the worst-case outcomes.
This insight can also help you mitigate fallout with customer relationships by offering them early notice of a delayed delivery and an accurate estimate for the new shipment date. Running scenarios can also help you decide which projects to prioritize. If you have a major client with a very sensitive deadline, it may be more critical to get their work done on time rather than reducing the overall number of late projects.
JobPack® can help your manufacturing business avoid disruptive downtime, and help you respond more nimbly if a crisis does occur.
Some amount of downtime is inevitable for most factories. However, that doesn’t mean all downtime is unavoidable. In fact, most of it can be prevented with the right planning and foresight.
By providing your manufacturing team with complete visibility into your production processes, you can forestall the brunt of these disruptions. And when a breakdown does occur, the scenario planning features of our software can help you find a solution. In fact, you can even use those features to create an emergency plan for major projects where unplanned downtime would cause a true crisis for your business.
JobPack®’s capabilities extend far beyond risk mitigation. In fact, our scheduling software can help your business become more resilient by increasing the overall efficiency of your factory. Contact us today for a demo of our product and to learn more about what we can do for you.