JobPack® has been specializing in digital solutions since 1992, so we understand the importance of connecting the right data with the right people to make informed decisions.
Case Studies
See how we give our customers the visibility to plan better, improve customer service, and ensure on-time deliveries.
All levels of your organization will benefit from the highly adaptable, efficiency boosting scheduling and analytics of JobPack®.
Our visually intuitive production scheduling solution will do more than make the plant and operations managers job easier, it will unleash the potential of your business. When integrated with your ERP system, the CEO will have greater insights, purchasing will make better decisions, and your IT staff won’t be burdened by additional tasks.
Need support pitching JobPack® to management?
We’ve got you covered.
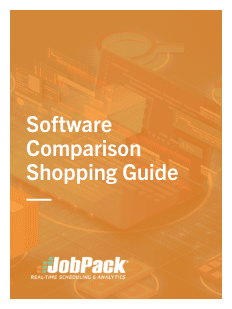
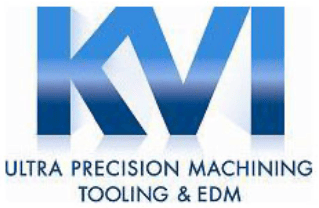
JobPack® gives us better accuracy on delivery promises. But even more important is that when there are problems, we see them weeks before projects are due so we have time to take action
About
KVI is an engineering and manufacturing company serving the medical device, pharmaceutical, and aerospace industries since 1977. KVI possesses the skills, knowledge and experience to meet the most demanding requirements, from prototype to production.
Why JobPack® works for us
“We have a complex organizational structure with four separate business units functioning under one roof: tool and die, wire and brand EDM, full production CNC milling, and production turning. Our lead times ranged from 24 hours to six months and a spreadsheet just wasn’t feasible anymore. Plus, the scheduling solution within our job costing and management system was neither flexible nor adaptable. One of the greatest things about working with JobPack® was their flexibility with understanding our needs and ability to come up with custom applications. We never got pushback, and there was always a proactive approach to solve a need or answer a question.”
“When they delivered our on-site training, they didn’t just teach the us how to run it, but they spent time with our people on the floor, coaching them. One absolutely huge benefit of using JobPack® is being able to see the whole picture of each job every day. We really have a handle on solid dates now, taking into consideration all the constraints, whether it’s outside services or internal labor on a particular job. Just having that viewpoint from 30,000 feet is a big help in providing better answers on lead times to our customers. And, it gives us better accuracy on delivery promises. But even more important is that when there are problems, we see them weeks before projects are due so we have time to take action.”
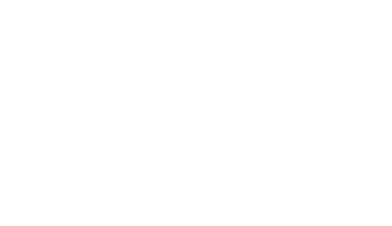
We literally couldn’t run our dynamic and growing manufacturing operations without JobPack®
About
Bluco Corporation has been the leader in precision modular fixturing for welding, machining, and assembly since 1990, delivering the highest quality components, tables, services, and solutions.
How JobPack® meets our needs
“As we grew from one machine to three and our customers were asking, ‘When will my order be completed and shipped?’ we realized we couldn’t manage effectively with the spreadsheet we had been using. We couldn’t do scenario planning. Every time something changed, we had to change every other cell in the spreadsheet. It just becomes unmanageable. We sat through demos from other software companies, and found JobPack® had the best scheduling interface. Plus, we were looking at integrating our ERP data and we spoke to other JobPack® customers, ultimately deciding it would be the best fit for us.”
“Because of the graphical interface, we are able to ‘drag and drop’ jobs around to ultimately optimize the schedule. We have several different roles in our facility using JobPack®, and everything was described in our training very accurately. The trainer had been a user of the software as a customer for many years and they showed us not only how to click the buttons but also how they solved this problem and how they handled this type of process. It was very insightful. We simply couldn’t run our dynamic and growing manufacturing operations without JobPack®.”
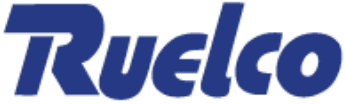
Once we had grown big enough to staff production manager, engineering, and machine operator roles, we needed to communicate the status of jobs to everyone. JobPack® gives us a streamlined production methodology
About
Ruelco features a fully operational and fully integrated, climate controlled 60,000 square foot machine shop in New Orleans, Louisiana. Ruelco has an ISO9001 certified Quality Assurance and Quality Control program that enables them to provide only the best parts to customers.
How JobPack® helps us scale
“At first, we had a non-automated process on paper. But once we had grown big enough to staff production manager, engineering, and machine operator roles, we needed to communicate the status of jobs to everyone. JobPack® gives us a streamlined production methodology more based on how much time we have and what we need, as opposed to working from out-of-date spreadsheets. From the beginning, JobPack® did everything on a more personalized level with us, unlike the competitive software solution providers whose approach felt canned. JobPack® understood our problems and provided effective training. Other production schedule providers expect everyone to fit in their box, as though the software they developed will work for everyone. But they don’t really tell you how.
JobPack® works with us to customize reports and change things that need to be updated. Now, everybody has a better idea of the bigger picture. We know if we have tooling, material, and parts, and we know what days the jobs need to be done. From the perspective of the people on the floor, they like having more insight into what’s going on as opposed to just being handed a job packet. It lets them be more effective at their job in a more timely fashion.”

Production Scheduling

Machine Monitoring
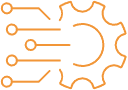
ERP Integrated Data Analytics

Intuitive Interface

Modular Solution
