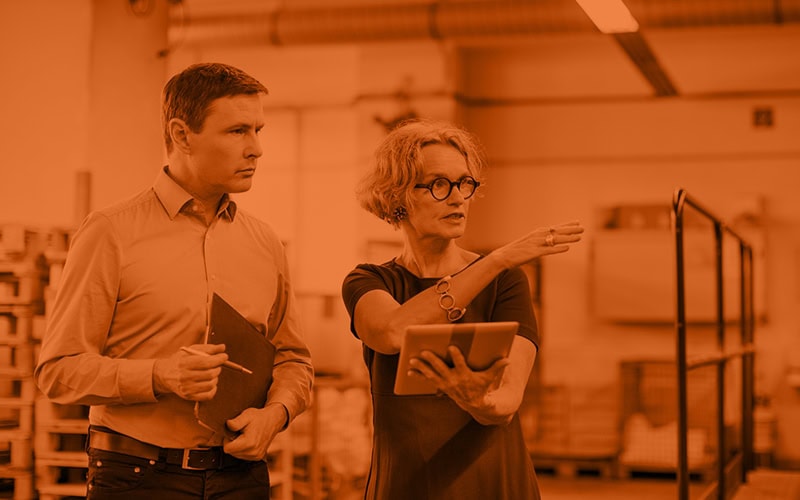
4 Ways JobPack® Improves the Bottom Line for Manufacturers
Scheduling and machine monitoring systems have a direct impact on a business’s financial health.
When manufacturers think of ways to improve their bottom line, it’s a safe bet that their scheduling system isn’t the first operational tool to spring to mind. Scheduling software is often considered an overhead expense—a program necessary to keep the shop floor running, but not a make-or-break factor with significant financial ramifications.
However, many of those same manufacturers report levels of chaos and disorder on the factory floor that frequently lead to missed delivery dates and an environment where managers feel they are constantly managing production emergencies with no knowledge of how or why they’ve begun.
Our experience in the manufacturing industry provides an answer. Production floors are in disarray because they lack both the scheduling software and the machine monitoring tools to provide accurate delivery dates and real-time insight into how well the actual production process is matching the production plan. JobPack®’s combination of scheduling and machine monitoring software gives manufacturers that much-needed visibility. Here’s what our software can do for you.
1. Improve on-time delivery rates.
It’s difficult to determine a standard on-time delivery (OTD) rate for the manufacturing industry, but it’s not uncommon to see OTD rates hovering in the 70% range. Many shops struggle to cross the 90% threshold. The difficulty of hitting a high OTD rate seems so universal that many shops have little motivation to improve.
But what if you could reliably promise an OTD rate of over 90%? Not only would this set you apart from the competition, it would reflect a real improvement in operation efficiency within your shop.
JobPack® improves on-time delivery rates by helping your schedulers create a production plan based on a more complete list of steps and processes. Our program displays this information in a color-coded calendar that makes it easy to see at a glance when production is running behind, and make needed adjustments to get the schedule back on track.
How does this improve the bottom line?
Falling behind on delivery dates can cause production backups, limit your ability to take on new work, damage faith with clients, and even incur financial penalties due to broken contracts.
2. Reduce overtime with insight into production schedule and capacity.
Many manufacturers, faced with a production delay, try to solve the problem by approving overtime. They may even take on work which they know is above their normal capacity on the assumption that additional overtime can make it all better.
However, overtime doesn’t fully account for every bottleneck or production step. By stacking on overtime without complete insight into production capacity, manufacturers can quickly find their delivery dates falling behind like a stack of dominoes. JobPack® keeps these other factors in context, showing manufacturers exactly how additional overtime will affect their delivery rates.
How does this improve the bottom line?
Overtime pay adds to operating costs and contributes to worker dissatisfaction. Operating above capacity can worsen bottlenecks and lead to missed delivery dates.
3. Provide an overview of machine use for maintenance and purchasing decisions.
Many manufacturers know where their bottlenecks occur, but they don’t always know how to resolve them. A common solution—purchasing another machine—can relieve the issue where it occurs, but may not solve the underlying causes, which are a scheduling problem. For example, if your scheduler can see that multiple orders will require the same machine, they can start some projects earlier so that the machine use is spaced out over several weeks, sparing you the purchase of a new machine.
Machine monitoring is another overlooked software tool for improving factory performance. Not only does monitoring software help manufacturers track the progress of projects along the production line, it also helps identify which machines are over- or under-used. If you can see that certain machines are running at full capacity throughout the working day, that’s a sign that you may need to consider expanding your capacity by purchasing another machine.
Finally, few disruptions are more frustrating than unexpected downtime on the factory floor, especially when it’s due to a breakdown of machinery. Proactive maintenance can avoid a breakdown during an inconvenient moment, but it’s still unavoidable downtime. Scheduling and machine monitoring software can help you identify where to plan maintenance so that it is least disruptive to your schedule.
How does this improve the bottom line?
Identify where purchasing additional machines would improve capacity. Schedule proactive maintenance during known downtimes to avoid disruption.
4. Enable more effective inventory management.
Manufacturers need to have supplies of certain raw materials on hand in order to handle their production process. Running short on a critical material can lead to unexpected downtime, leading to missed delivery dates. Under-stocking can also leave a business vulnerable to broader disruptions in the supply chain.
At the same time, over-stocking supply comes with its own problems. Inventory can expire, grow obsolete, or become damaged while waiting to be used. Over-stocking means businesses are paying more up-front for warehouse space to store materials they don’t yet need.
JobPack®’s software helps manufacturers see exactly what materials they will need to have on-hand, and when in the production schedule they are planning to use them. That insight can help manufacturers order inventory based on what they know they will need, rather than their best guess.
How does this improve the bottom line?
Avoid over-stocking inventory before it is needed, and prevent inventory shortages during crucial production times.
JobPack® gives manufacturers visibility into their factory floor operations so they can eliminate blind spots and reduce unknowns.
If we could summarize what JobPack® provides manufacturers in one word, that word would be visibility. The manufacturing industry has only grown more complex, and there are too many factors at play for anyone to keep track of on their own. Even those most adept at planning through spreadsheets or other analog means are making their work harder than it needs to be, and missing out on real-time data in the process.
By offering a more comprehensive overview into production capacity, JobPack® gives manufacturers the information they need to make effective leadership decisions for their companies. It’s not hard to trace the effects of our software back to measurable bottom-line savings. Contact us today if you would like us to demo our software for you.