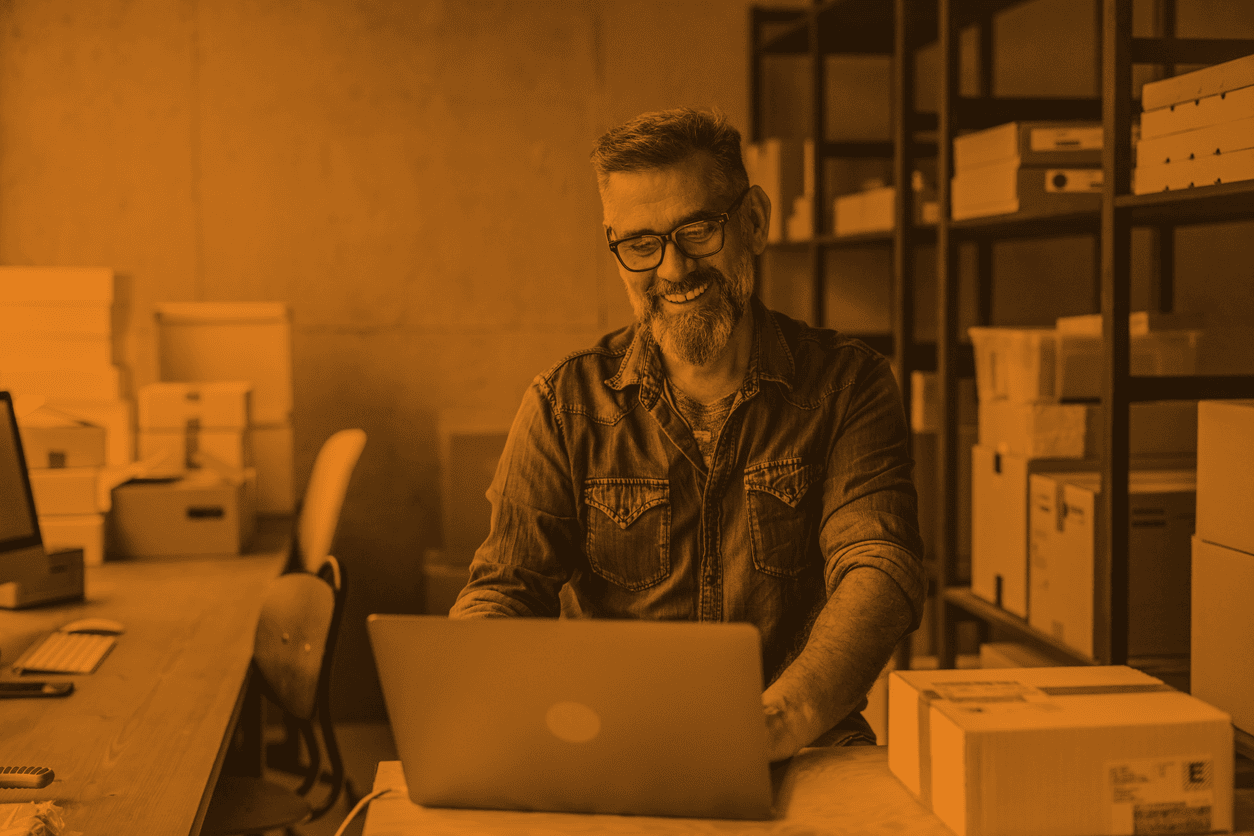
5 top things to look for in a scheduling and analytics system
When you are choosing a Manufacturing Execution System (MES) to run every aspect of your shop, look for one that gives you complete accuracy, visibility into your machines and personnel, real-time responsiveness, flexibility to work like you do, and simplicity to make it readily accessible to everyone.
ERP systems cover many areas within a business that can help streamline operations: order processing, payments, accounting, and CRM functions. But more often than not, the scheduling module (if even offered) is something that seems impossible to setup, impossible to use daily, and impossible to get any relevant and real information out of.
In working with many different ERP systems over the years, and integrating a separate MES into these packages, I have come to realize that the ERP system was often built up around the financials module. After all, it’s the financial module that gets the big deals done. The issue this presents is that the ERP modules are built around accounting and as a result do not work with the MES or scheduling module. Accountants set up and justify costs based upon the other functions of the ERP system — quotes, inventory, and profitability — but planned times, machine run rate and costing rates typically are calculated differently on the shop floor versus what is defined in the financial modules. As these modules are all tied together, it’s nearly impossible to receive real scheduling data to perform planning, estimate delivery dates, or get a true indicator of internal operating costs.
So, what is a Production Planner to do?
You could spend time trying to wrestle with your ERP system’s scheduling module, but chances are you’ve already tried this and realized quickly that this will not work. You could resort to the Excel spreadsheet, but there is also a very good chance you were doing this alongside trying to use your ERP. The pitfalls as you probably already know are: it takes a long time to maintain, everyone has a different copy, its outdated the moment your done compiling it for the day, there’s no long-range planning, and worst of all the data is incorrect and static.
It’s time to take the MES Scheduling leap
An MES needs to be able to give you:
- Accuracy: Provide accurate dates of when production orders will complete
- Visibility: Provide indication of bottlenecks within the production process
- Responsiveness: Adjust based on finite capacity information and operator feedback
- Flexibility: Accommodate various scenarios with production
- Ease of use: Be easy to use for the end user
What to look for
Accuracy: When talking about scheduling or production planning, the ultimate goal is to know when jobs will really start and when they will really finish. This leads to the most important aspect of all: providing correct delivery dates to the customer. In order to obtain accuracy, you must have correct data such as correct routing steps and planned times. That doesn’t mean you must have these things nailed down prior to purchasing a system. If you need to gather accurate times, find a system that has a mechanism to clock operations in and out so you can collect the real-time data for the next time you run the job. An effective MES system must be built upon finite capacity and move in real time starting with today’s date and moving forward.
Visibility: Visibility within the system is key. The user needs to be able to identify where the job is, where it will be, and any changes that are occurring based on other work around it. The MES should also have the ability to easily identify any late jobs before they are late. If all you are presented with is pages and lists of data, it is extremely time consuming to identify what is happening and why. The scheduling tool should be visual in its calculation of jobs and operations.
Flexibility: Flexibility is required so you can alter the course when needed to keep those promised delivery dates. I’m not talking about adding a 25th hour to the day, but flexible to the point where you can run scenarios and see the net outcome immediately. Manufacturing is anything but static. So if you can’t adjust your schedule and see the results right away, not only will the information have changed by the time you see the outcome but its wasted time waiting for the system to recalculate. A good MES should be able to run various scenarios within realistic parameters to see how that impacts your customers’ orders. If you can’t do this, then you are no better off than when you were running Excel as your main component for production planning.
Ease of use: This one sounds like a no brainer but is probably the most overlooked function of a system. You can have the best scheduling program in the world, but if your users are scared of it or can’t get their heads around how to use it, it’s useless. A good system can provide the previously mentioned attributes but still be simple enough to understand how it performs them. Make sure you can easily identify what data will be required for the system, how to run a scenario, how to undo a change, and where to get the highlights such as real delivery dates, work queue, and what jobs are late before they are due.