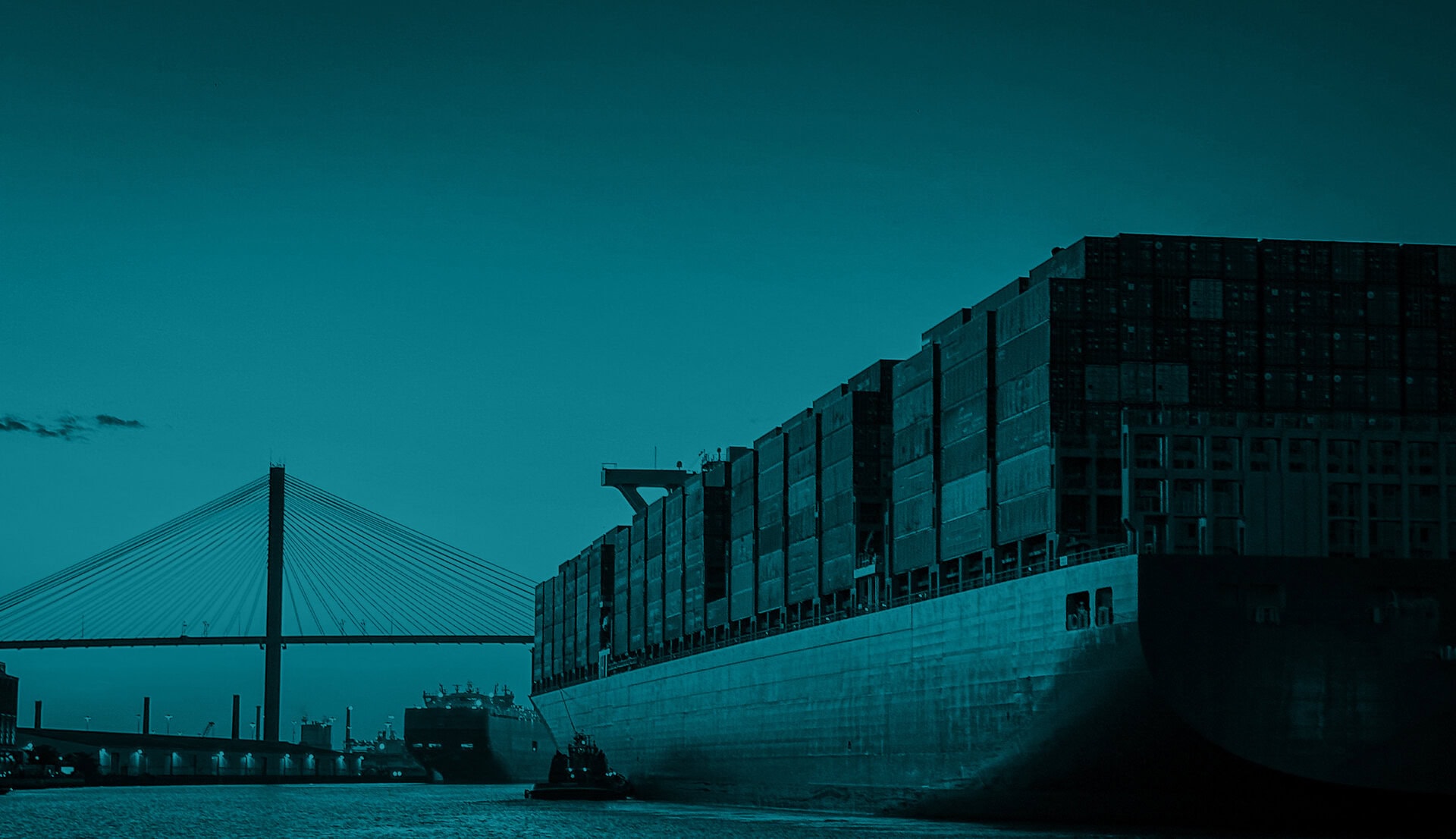
An ERP is the brain of your organization. An MES is your hands. We can connect them.
When it comes to the large-scale functioning of your manufacturing business, your Enterprise Resource Planner (ERP) calls most of the shots. It has broad oversight of the data that keeps your business ticking, from accounting to HR to supply chain management. In a way, it’s the brain of your organization, and probably the tool you’ll refer to most at high decision-making levels.
But your Manufacturing Execution System (MES) is the tool you need to execute your projects on the shop floor. It’s the software directing the real-time operations and giving your managers the feedback they need to run effectively. If you want to get the most from these two systems, you need to connect your brain to your hands.
Of course, most manufacturers understand this intuitively. That’s why one of the most frequent questions we hear when talking about our MES is “will it integrate with my ERP?”
The short answer is: Yes.
We can connect to your ERP. It doesn’t matter what system you’re running—as long as it has an API, we can connect to it.
If that’s as much of an answer as you need, contact us! We’re ready and waiting to give you more details about our product and can even schedule a demo with your team to show you the specifics.
However, we’re aware that a simple “yes” isn’t enough for many companies, especially those that have been made promises in the past that didn’t live up to reality. Businesses have a right to be skeptical, especially if they earned that skepticism from having gone down that path before.
So, if you’re interested in more details, we’re happy to share those, too. Read on as we dig in.
What ERP systems do you have experience with?
We’ve been in this business a while, and there are few ERP systems we haven’t met—and none we haven’t been able to integrate with. The ERPs we encounter most frequently include:
- E2
- Globe
- Great Plains
- JobBoss
- Microsoft Dynamics
- RealTrack
- SAP & SAP Business 1
- Sage & associated products
…and more.
That said, every business is different, and no business uses their ERP in exactly the same way. Their processes, products, and personnel all vary, which means that by either choice or necessity, they’ll each have developed different ways of creating, storing, and tracking their data.
This means that every integration of JobPack® is a custom integration. Our first task is to get to know how your company operates so that we can write our interface to meet your needs. Once we understand how the data is coming out of your ERP, we can put it into JobPack® and enhance your operations.
How long does an integration take?
Six weeks.
From the day of purchase to day of production—all of which includes installing the software, doing the consultation, writing the interface, pulling the ERP data into JobPack®, and sending a trainer to your location to show your team how to use the program and optimize the software—that whole process can be done in as little as six weeks.
That number can change based on a few factors. If your team isn’t available, if you have special requirements, or if your needs change during the implementation as you discover more about the software capabilities, then these conditions can lengthen the implementation time.
Nevertheless, we’re pretty proud of our turnaround time. We’ve seen large ERP implementations take as much as five years, with specialists called in to consult on the project driving up the costs.
By contrast, our system doesn’t technically need an ERP to run. If you’re just looking for a scheduler, you can be up and running the day of purchase. Integrating with your ERP is simply a more efficient way to import data.
What if we don’t have the IT staff to support the implementation?
We work with manufacturers of all sizes. Many of the smaller job shops we work with don’t have IT staff on hand to help with the implementation. We’re proud of our ability to come in and provide these businesses with the IT support they need to get the implementation up and running.
This means getting a database server set up with SQL, installing the software on the server, setting up security, and then linking everything to the client’s desktops so that their team can access the software and see the information. There’s a lot of moving parts involved, but that’s the benefit of having a team member on-site. We can make sure all our clients’ needs are met, no matter the size of their operation.
JobPack® + your ERP = a more efficient shop floor with greater throughput.
At the end of the day, our clients turn to us because they want to see efficiencies flowing from their top-level decision-making programs all the way through to the execution on the shop floor—from their ERP brains down to their MES fingertips.
That’s what we’re here to solve. In an industry where margins are tight and production deadlines need to be met, data is too precious to be left wasting away in silos. By integrating your data across your systems, we can help your business unlock systemwide efficiencies.
A more productive shop floor is weeks—not years—away. If you think your team can benefit from a scheduling solution that combines machine monitoring with insightful reporting, contact us today. We’ll discuss the details of our software with you and schedule a demo so that you can see how it works firsthand.