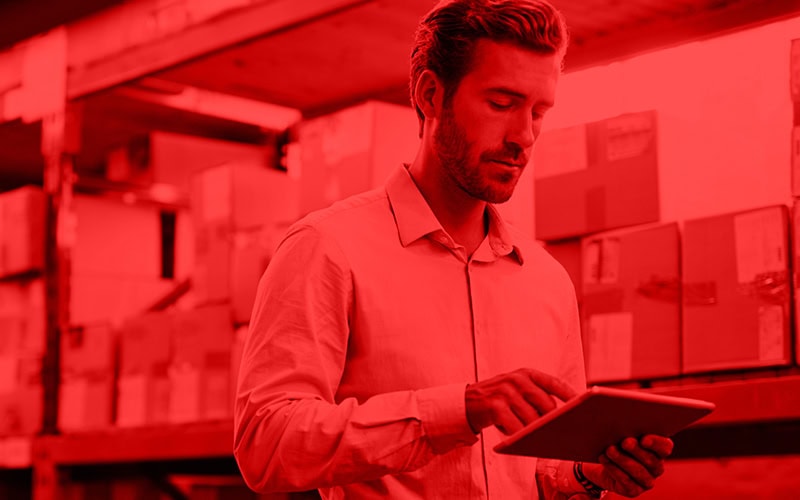
Job shops have fewer resources and little room to spare. JobPack® can help them get the most out of what they have.
When it comes to manufacturing software, many solutions are built with large production shops in mind. The expense of these systems, as well as their superabundance of features, makes them a poor option for smaller operations, especially those who specialize in small production runs or one-off jobs.
At the same time, small manufacturers have as much to gain from manufacturing software as larger shops. That’s why we’ve developed JobPack® as a niche product that can integrate with the ERP infrastructure of larger manufacturers while also solving the very real scheduling needs of smaller shops. In doing so, we’re helping manufacturers of all sizes become more efficient with their production management. Here’s how our product is especially valuable for job shops.
1. Reduce the time spent scheduling and managing projects.
Job shops rely on various methods for managing their production schedule ranging from spreadsheets to magnets on a whiteboard. However, these methods often fail to capture every step in the production process, and as a result, production managers have to devote extra time to correcting for a real-time schedule that did not match what they had planned on paper. If the production schedule goes really off the rails, they may spend additional hours trying to diagnose what went wrong—with no guarantee that their solution will prevent similar problems from happening in the future.
JobPack®’s scheduler helps production managers account for every variable. With the correct lead time in their planning system, they can create an accurate schedule the first time. That’s less time spent redoing the production plan later, and no time lost to fruitless searches for root causes that can only be discovered with more data.
2. Understand your actual machine use data.
In the data age, many of us have become accustomed to a surplus of knowledge. However, many small shops are missing key data on the very tools that keep them running: their machines. The data offered by machine monitoring software can answer many key questions that can inform higher level decision making.
For instance, you may have noticed that you frequently experience backups at your lathe. The simple solution may be to buy a second lathe to relieve the bottleneck, but with machine monitoring installed, you realize that your lathe actually runs idle for long periods in between projects. The bottlenecks aren’t caused by a lack of capacity on your lathe, but by production schedules that frequently cause several projects to hit the lathe at the same time. By adjusting your schedule, you can resolve the bottleneck without having to make a major capital expenditure.
3. Eliminate paper waste and storage costs.
Manufacturers who still rely on paper packets to run jobs aren’t just contributing to clutter in their work environment—they’re also paying extra for paper, toner, printers, print repairs, and file storage. While these aren’t the most significant operating expenses, they do add up, year after year.
JobPack® offers a fully digital solution to production floor scheduling. Digital packets make it easier for manufacturers to keep production information in one place and track design changes while also eliminating the need for a separate digitization process. By storing digital packets in the cloud, JobPack® also makes it easier for manufacturers to run one-off or custom projects.
4. Gain greater insight into your capacity.
Every job shop owner knows how hard it is to gauge capacity. While no business wants to turn away work, it’s equally risky to take on more than your workers can handle. At best, you may end up paying extra for overtime labor, and at worst, you may end up running late on projects, missing delivery dates, and losing customer trust.
By offering more robust insight into your overall capacity, JobPack® can solve both these problems. With a clearer understanding of your workload, you won’t have to choose between turning down work you’re not sure you can handle or accepting jobs that will put you behind on your other commitments.
5. Avoid unexpected downtime.
Machines need regular maintenance to avoid breaking down, but scheduling maintenance can be a challenge during busy production hours. As a scheduling tool, JobPack® helps manufacturers spot windows of opportunity where proactive maintenance can take place with minimal disruption.
6. Manage your inventory more efficiently.
Small manufacturers who specialize in short production runs or custom projects have an especially difficult time managing inventory. Too much stock takes up warehouse space, and if product expires before it is used then it contributes to overall waste. Too little stock can leave a manufacturer short in a critical moment and cause a project to be delayed.
By providing greater oversight into upcoming projects, JobPack® eliminates the guessing game, allowing manufacturers to order in new stock as it is needed and not before.
JobPack® offers a quick implementation and training turnaround compared to more cumbersome ERP systems.
In an age of growing digitalization, many job shops may feel the pressure to move to digital systems simply because everyone else is. However, manufacturing software wouldn’t be so essential if it weren’t providing quantifiable competitive advantages. And with a solution like JobPack®, small manufacturers no longer have to worry that these benefits are only available to large production shops.
In fact, unlike many ERP systems on the market which require twelve to eighteen months and extensive training to onboard, JobPack® can be up and running in six weeks and requires relatively minimal training. Moreover, if you already have an ERP system installed, our product can integrate with it and supply the missing link between your larger resource planning and your shop floor.
Contact us today to learn more about how we can supply the solutions your job shop needs to thrive.