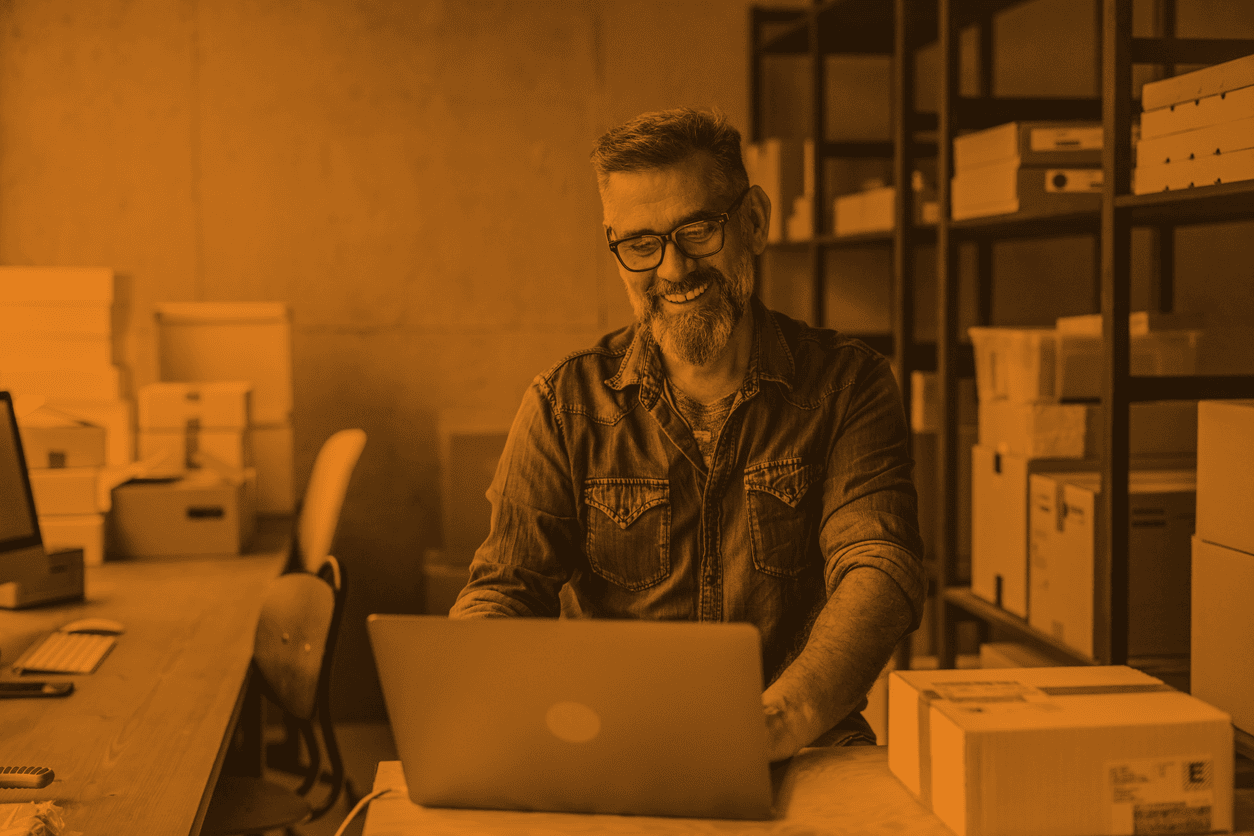
Managing an active manufacturing floor demands a scheduling tool that can keep track of every contingency.
Machine scheduling in a manufacturing environment often feels like a losing battle. With dozens of machines performing different operations, outside vendors with their own production schedules, and customers with varying needs and expectations, few shop floors are ever running exactly to plan. And yet, manufacturers depend on their ability to deliver work reliably and according to schedule if they are to maintain trusted business relationships.
If the confusion surrounding production floor scheduling could be reduced to a single word, that word would be “visibility.” Manufacturers simply do not have enough operational oversight to anticipate delays, head off bottlenecks, or accurately gauge capacity. Part of the problem stems from the fact that many manufacturers are still running their operations on basic spreadsheets or even with magnets on whiteboards, which are not able to capture the complexity of factory operations.
JobPack® resolves this problem by delivering a scheduling tool that finally offers a full accounting of the production process. With a user-friendly visual interface that shows how jobs are linked, and “what-if” scenario planning functionality that helps managers forecast the impact of different scheduling solutions, manufacturers can plan their operations with confidence that an unknown variable won’t throw a wrench into their scheduling.
To demonstrate, we’d like to share five common scheduling problems faced by manufacturers, and how JobPack® provides a solution.
1. Multi-step processes are not properly accounted for.
Some manufacturing processes are simple, with only a step or two required to complete the job. Others are more complex, with additional heat treatments, chemical coatings, and finishing processes—and in some cases, entire sub-assemblies.
JobPack® shows which separate jobs are part of the same order, and what kind of impact changes to the schedule will have on the job status. You will be able to adjust jobs so that all related steps stay in the correct process order.
The drag-and-drop user interface makes it easy to move jobs earlier into the schedule. Other jobs in the order will automatically adjust.
2. Last-minute rush order.
Good customer service comes in many forms, and one of them is the ability to manage a last-minute order. In order to accept this work while building customer trust, manufacturers need to be able to see whether they have the capacity to accept an order. However, gauging capacity is not a straightforward process
For instance, maybe you don’t have capacity if you run your machines according to their regular schedule, but you can fit the job in if you run some overtime. Or maybe it only looks like you don’t have capacity because of how your jobs are ordered. The process of rearranging work can create holes in your schedule that aren’t immediately apparent.
After making adjustments, the “Fill Holes” function tightens up the job schedule to automatically create a more efficient work order.
You may also decide that finishing late on some minor jobs is an acceptable tradeoff if it allows you to make a larger, more important deadline. JobPack® will show you how many days late you are on an order, and how much your schedule adjustments have affected delivery dates.
3. Inability to accurately predict capacity.
Another way JobPack® helps manufacturers judge their capacity is through our capacity window. This tool provides an easy visualization for your overall workload over a period of time. Manufacturers can see which tools are at capacity, and can forecast how long they are likely to remain so.
The sliding window offers a user-friendly interface, and can be adjusted to show larger or smaller periods of time.
The capacity window also helps manufacturers judge when it is time to order new machines. If you expect to be running your laser at 100% capacity for the foreseeable future, but also expect to bring in work that will require this tool, then the capacity window can show you whether it’s time to make a new purchase or find an outside supplier to handle your overflow.
4. Vendor schedule doesn’t align with work order.
If you work with outside vendors, it’s likely you’ve gotten tripped up over this problem before: you plan your schedule assuming they share your hours of operation, but fail to account for some eccentricity in their operations, such as only delivering on Tuesdays, or only being available Wednesday–Friday.
A slip-up like this can put you back a full week if you miss the cutoff, and a delay like that can cascade into more problems as your overdue job begins to run into projects that had previously been running according to schedule.
Our scheduling tool helps account for these scenarios by offering detailed settings for external work orders. You can set the number of days a business is open in the week, the number of hours they’re open for, and which days they’re available.
5. Too many projects finishing late.
Sometimes, despite your best efforts, something goes wrong and you’re running behind schedule. Maybe a machine broke down, or a supplier was late delivering an order, or one of your operators called in sick. Whatever the case, you need a way to make up ground.
Running overtime is not a long-term solution, but it is sometimes necessary to get all the work out the door. But before you approve overtime hours, you want to see if that work will have the effect you’d hoped for. Otherwise, you may run a bunch of overtime and still find your work coming in late.
JobPack®’s scheduler allows you to see the effects of increasing overtime on each machine in your shop. Set the additional hours and the number of days you plan to run, and see how the results impact your delivery dates.
JobPack® will show which jobs are now coming in on time, and by how much the change affected the delivery schedule.
JobPack® offers a clearer image of lead times, capacity, and other scheduling factors so that you can eliminate unknowns and plan with confidence.
As we’ve shown, a wide range of scheduling errors have a common root cause: lack of visibility. Our software is like a combo tool: a magnifying glass to identify problem areas that are often overlooked, a telescope to anticipate capacity overloads before they reach you, and an X-ray to cut through all the complexity so that you can gain a clear picture of every layer of your operation.
If you would like a full demo of our software, we’re here to help. We can run through scenarios similar to the issues shown above, or even work with your factory data to showcase how our system would handle your current operations. Contact us today to get started.