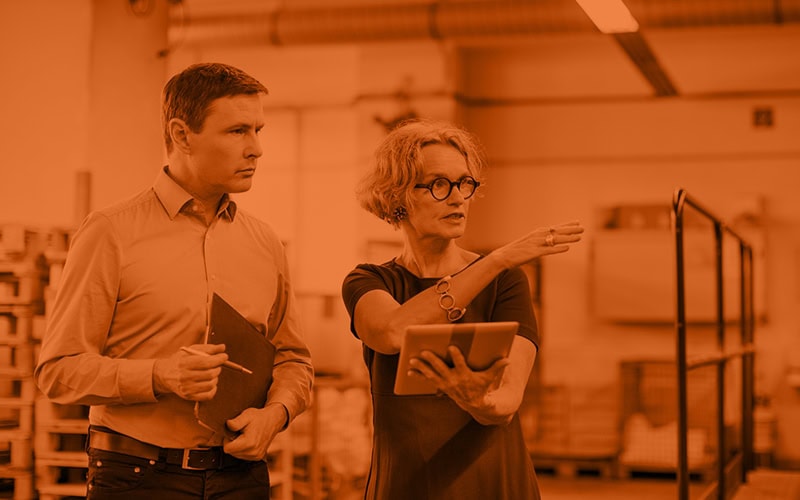
JobPack® modules help manufacturers purchase exactly what they need without creating redundant systems.
It’s not news to anyone that the state of manufacturing software is highly fractured. Few “all-in-one” products deliver truly comprehensive software packages, and those that do often fall short in terms of providing solutions that actually fit user needs. In other words, one part of their product may work as advertised while another part is left to languish. On the other end of the spectrum are software solutions that do one job, and one job alone, leaving key functions unfulfilled.
At JobPack®, our goal is to offer the best of both worlds. We’re here to integrate with the systems you have, and fill as many of the gaps that are left. And rather than sell our product as an all-in-one unit, we’ve created a modular system where each component can function independently, or in conjunction with the other units. So, whether you want to purchase only the modules you need or invest in the complete system, the business decision is yours. Here’s what we have to offer.
JobPack® Scheduler
Many manufacturers are still trying to run their production scheduling using Excel spreadsheets, or even with magnets and dry erasers on whiteboards. These tools make it cumbersome to move jobs or adjust schedules, fail to account for variables that cannot be easily tracked in a spreadsheet or on a whiteboard, and introduce greater opportunity for human error.
Many ERP systems also offer manufacturing schedulers in various forms, but these often carry over assumptions from the parent system that cause errors or discrepancies in the scheduler. As a purpose-built scheduling tool, JobPack® accounts for more conditions and variables, while providing seamless ERP integration.
Features of this module include:
- Real start and end time dates. Schedule with confidence knowing that your system is giving you accurate timelines.
- Future capacity data. See how far ahead your production is booked and where your next window for new work opens.
- What-if scenario planning.
- Planned schedule. Once you have a schedule worked out in the tool, all you have to do is hit save to put that schedule into action.
AIR Work In Progress (WIP) Tracking
While the scheduler sets the plan, the WIP module provides real-time feedback about how that work is progressing. The insight provided by the WIP module helps manufacturers improve their on-time delivery rate by identifying areas where the production schedule doesn’t align with the shop floor, and deliver more accurate estimates by accurately accounting for the time spent on a project.
Features of this module include:
- Work queue. Machine operators can clearly see what jobs they are scheduled to work on, as well as the priority order.
- Work list. The WIP module provides operators with a list of all parts needed to complete a project.
- Start and stop jobs. Jobs can be started or stopped directly from the WIP module.
- Part count records. The WIP module tracks how many parts are produced during a shift, and machine operators can update the record with details about that day’s performance.
- Actual time-to-completion. Manufacturers will be able to gather data about actual project time, leading to better cost estimates for future work.
AIR Machine Monitoring
The Scheduler sets the plan, and the WIP shows what actually happened, but you need machine monitoring to know why a project ran the way it did. Our module can show if a machine was running slowly, if the operator needed to stop and wait for an inspector, if the operator went to a training class, or if the machine was stopped for cleaning, maintenance, or repairs.
While our Scheduler and Machine Monitoring modules work independently, they also form an excellent combination when working together. Many of our competitors will focus on only the machine monitoring, without reference to the scheduler. But by looking at the data side by side, our module lets our customers see what they had planned to accomplish, how their operations aligned with that plan, and where the points of disconnect occurred. That feedback helps them remedy problem points and create a more effective plan in the future.
Features of this module include:
- Data aquisition from machines. Create a performance log for deeper analysis.
- Automatic and manual data gathering. Machine performance is tracked automatically while operators can also add notes to document performance.
- Uptime and downtime causes. Identify what caused machines to go down, and create a plan for managing downtime in the future.
AIR Analytics
Together, the Scheduler, WIP bookings, and Machine Monitoring all feed into Analytics. From this platform, manufacturers get a live overview of how the factory floor is performing against expectations. Along with the live views, Analytics can also create reports on KPIs and deliver insights to shop performance over time.
In this way, Analytics is an enhancement of other modules. Many manufacturers can’t give definitive answers about their factory performance, because they aren’t collecting the data. With data in hand, Analytics can finally help manufacturers understand what’s going on.
Features of this module include:
- Live status. See how jobs are progressing, which projects are meeting their delivery targets, and which machines are running slow.
- Historical analysis. Gain perspective on how your factory performs over time, with analysis growing richer as you gather more data.
- Reporting. Compile reports with visually intuitive charts that allow you to dig into the details on your machine utilization.
- KPI data. Track on-time performance, pass-through times, and overall equipment effectiveness (OEE).
AIR DNC & Paperless Manufacturing
Paper and manufacturing spaces aren’t a good mix. Not only does the paper get in the way and create clutter, it’s also hard to keep up to date and isn’t immediately accessible. With our DNC and Paperless Manufacturing module, operators on the shop floor can receive detailed instructions directly from engineers. A digital Jobpack® folder contains all part numbers and files associated with a job, and changes can be made electronically without needing to print out and deliver new documents.
Features of this module include:
- JobPack® creation. The module creates digital jobpacks to act as a centralized source of all production information and documentation.
- Per machine/part number. The module creates digital production records for traceability.
- Document revision control. Digital jobpacks reduce costs of waste and rework by ensuring that only approved versions are used.
- Send and receive NC programs. The module improves access to files, making it easier for operators to find the files they need.
We deliver the tools and insights our customers need to gain control over their factory floor.
At JobPack®, we believe that you should neither have to resign yourself to a substandard tool simply because that’s what came with your software package, nor purchase a whole new package just to get the missing piece you need for your shop.
Moreover, our WIP, Machine Monitoring, Analytics, and DNC & Paperless Manufacturing modules all run on our JobPack® AIR platform, which means you can access them from any device running a browser. By linking to an internal network, production data maintains an extra layer of security while still having all the benefits of wireless digital access.
If you would like to see how our product operates in detail, contact one of our service representatives. We would be happy to set up a product demo with your team and answer any questions you may have.