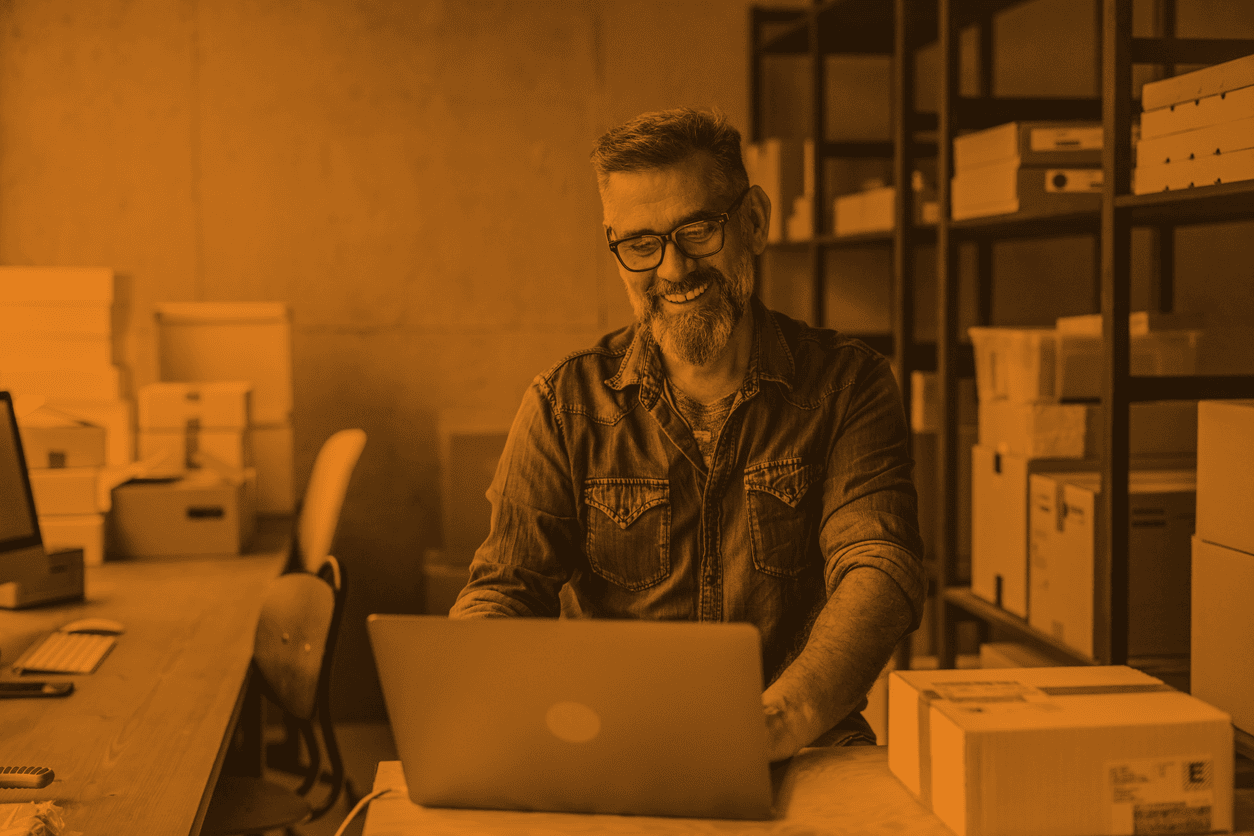
How Tracking on the Shop Floor Transforms Manufacturing Businesses
The insight manufacturers gain from monitoring tools is a game changer. Here’s why.
Ask a production manager the live status of their machines, and the answer you’ll hear from a surprising number of them is “I don’t know.” This is because many manufacturers have yet to adopt machine monitoring tools to aid in the operation of their businesses. Instead, many rely on the processes that have served them well enough so far. After all, if they didn’t need to know in the past, why should they need to know now?
The answer, of course, is because what you don’t know can hurt you. And for many manufacturers, these unknowns are slowly dulling their businesses’ competitive edge.
These unknowns include:
- Why a machine is running slow.
- Whether you have the capacity to take on another project.
- How soon your machine will be available to handle a new job.
- Why projects so often don’t run to plan.
- How accurately your projected timeline matches the actual timeline.
Many manufacturers think they have answers to these questions, but in reality, they have only theories. If you’re ready to replace guesswork with data, then it’s time to embrace the advantages machine monitoring can offer. Here’s what they are.
1. See your real-time job status from anywhere.
You’re in the front office and a customer calls with an urgent order. They want to know how soon their current round of parts will be ready to ship, and whether they can add another fifty parts to the order. In a shop without machine monitoring, answering this question will mean getting up from your desk and walking over to the factory to check on the status of the order. Or it may mean texting the production manager for an update and hoping he’s not on lunch break so you can get the answer quickly.
With machine monitoring, it means glancing at a monitor.
2. Spot underperforming machines and diagnose root causes.
When your shop is running slow, the sources of the slowdown are not always immediately apparent. Maybe there’s a bottleneck at one of the machines, indicating that you need a second machine to be more efficient. In reality, the machine isn’t the issue—it’s that there’s a process step that only one of your operators knows how to do, and adding another machine won’t double your machinists.
Or maybe the machine is running slow because its blade is dull, and you don’t need a second machine, just a new blade. Or maybe the backup is because the machine keeps producing irregular parts, leading to excess waste and extra rework costs. The point is: you don’t have to live with “maybe.” Not when you can know for sure.
3. Find opportunities for process improvement.
Are there slowdowns during your day that would provide a natural opportunity for routine maintenance? What about a redundant task that could be eliminated if you changed the order in which jobs are completed? Or a process inspection that could be more efficient if the inspector could check several machines in the area at once?
Machine monitoring can give you a better sense of the day-to-day workflow on your shop floor, drawing attention to areas of efficiency as well as areas of slowdown.
4. Gather data for long-term analysis.
How accurate are your estimates? What percentage of your projects were finished according to your job schedule? Are there certain kinds of projects that run smoother than others? Is there a time of year when your on-time delivery rate drops? How early in the season should you begin scaling up your operations to handle the increased workload? Can you measure your Overall Equipment Effectiveness?
In order to analyze the answers to these questions, you first need data. Data from your scheduling software can tell you the plan, but machine monitoring data can tell you what actually happened.
5. Eliminate sources of confusion and suspicion among your team.
Finally, when projects don’t go to plan, getting to the bottom of it can often feel like a lot of blame going around. The production manager wants to know why the operator left work before the job was finished. The operator insists they couldn’t finish the job that day because they were delayed for an hour and a half waiting for an inspection. The production manager is frustrated that there always seems to be a different excuse. The operator is upset that their work is being called into question.
This level of mistrust can quickly poison a work environment, and there’s no need to let it fester. Machine monitoring can offer a record to show what factors are causing frequent delays and not only resolve any dispute, but prevent them from forming in the first place.
Oversight at a glance will answer your biggest unsolved questions.
With the current rate of technological advancement, there are very few areas of your manufacturing business that should be a mystery to you. In fact, the tools at your disposal mean you have more opportunities to understand the inner workings of your business than ever before. Major business decisions shouldn’t have to rely on guesswork—not when the tools that could provide you the answers are at your fingertips.
At JobPack®, our machine monitoring module can deliver the insight you need to lead a more efficient business. Combined with our scheduling tool and analytics module, it can transform the way you see your business. Contact us today to learn more.