Yes, we use MTConnect protocols to gather data from the machine. We can also configure an unlimited number of fault reasons to be defined by the operator so you can gather machine info and identify external reasons when machines are idle or waiting.
Resources
Frequently Asked Questions
Quick answers to the most commonly asked questions.
Our goal is to make your experience as streamlined and simple as possible. Below is a list of frequently asked questions by those interested in improving their approach to production scheduling. We would be happy to answer any specific questions you may have.
Capabilities
Does JobPack® utilize MTConnect to gather data from my machines?
Can JobPack® capture machine events and machining time?
Yes, JobPack® provides machine monitoring for both new and legacy machines to capture uptime and downtime. You can use this data to look at key downtime reasons and start making the biggest impact to your efficiencies right away.
Will I have to manually schedule the work in JobPack®?
JobPack® will optimize you schedule to hit as many delivery dates as possible within your normal working business hours and capacity, and load machines so they are not sitting idle. That means you get more work out on time in the same number of hours so you can invoice more dollars.
What makes the JobPack® Scheduler different from other scheduling tools on the market?
Our main focus has always been production scheduling. We have refined our software for over 18 years to accommodate a wide range of scenarios. We provide our customers with the relevant data and real schedule dates for orders.
Do I need to replace my ERP or existing software to use JobPack®?
No, we can import the data we need for scheduling from your existing ERP. JobPack® can also run stand-alone.
ERP Integration
What is the basic data you need to be able to schedule jobs in JobPack®?
Basic work order or sales order info (part ID, quantity, delivery date) and basic routing/process steps. Routings can also be created in JobPack® and copied over the next time the same part is ordered.
Will I have to change the setup of my ERP in any way to use JobPack®?
No, JobPack® is versatile so that changes are easily made in our system to accommodate how your ERP was setup.
Do I need to add more detailed routing data to my ERP prior to using JobPack® if I want the systems integrated?
No, we can import as much or as little data as needed. If you do not have all the details in your ERP we can fabricate the data upon import, or the data can be kept in JobPack®.
Support
Will I need to leverage my ERP vendor to import data into JobPack® from our ERP?
Our engineers integrate the JobPack® Scheduler with over 95% of our customers who have an existing ERP in place. We have many database schemas for the most popular ERP systems, so there will be no need for added costs from your ERP vendor.
How do I know if I need a Scheduling (MES) system versus an ERP?
Often times many of the issues you are having are caused by lack of visibility of a schedule. If you know exactly when jobs will start, finish, be affected by changes, etc., you can control inventory levels better, provide accurate dates to you customers, better turnaround from your vendors, etc. JobPack® scheduling can resolve many issues that are common to manufacturing.
What is a typical implementation time for JobPack®?
Since our main focus is scheduling we can install, import data (if required) and train the user in as little as 3 weeks from start to finish. On average implementation time requires 8-10 weeks.
Can you update JobPack® if we already have a shop floor data collection system?
Yes, JobPack® can supply you with its own data collection to update work order progress, or we can import the status of jobs from your existing system.
Will my planner(s) struggle to use and understand the JobPack® Scheduler?
JobPack® has an intuitive interface that your planners will understand with ease. Sign up for a live demo to see how easy but effective our system can be through its easy-to-use graphical interface.
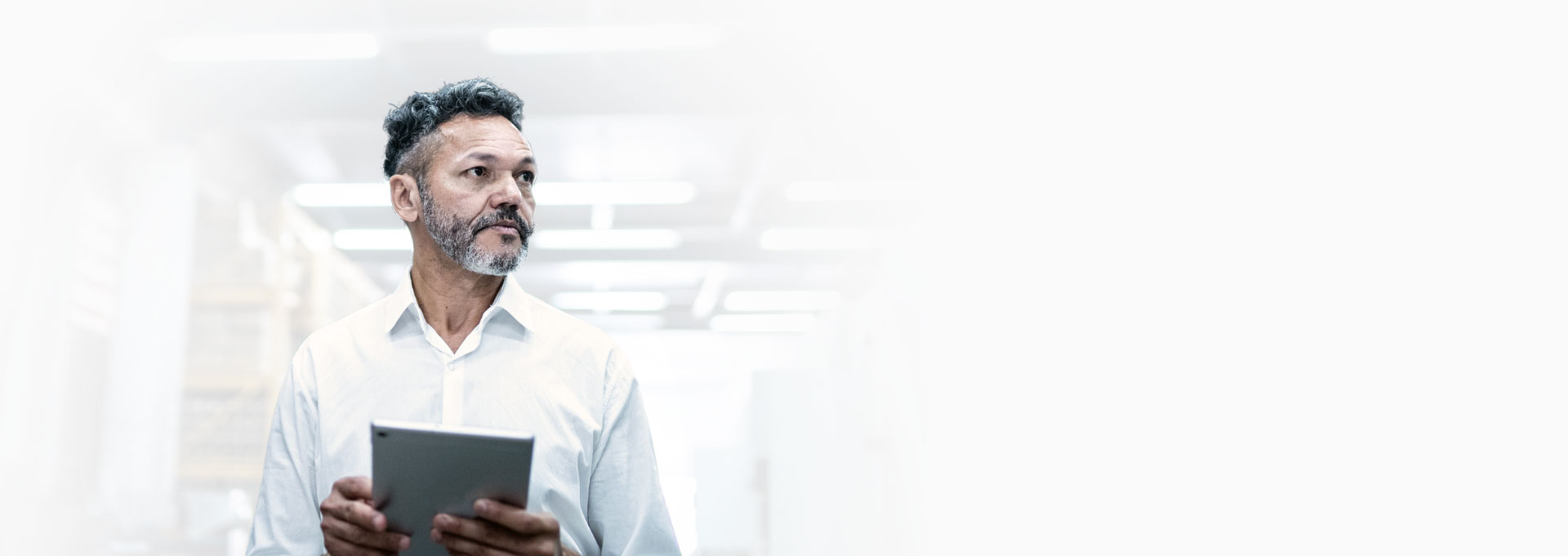
JobPack® gives us better accuracy on delivery promises. But even more important is that when there are problems, we see them weeks before projects are due so we have time to take actionKVI Ultra Precision Tooling & EDM See Success Stories