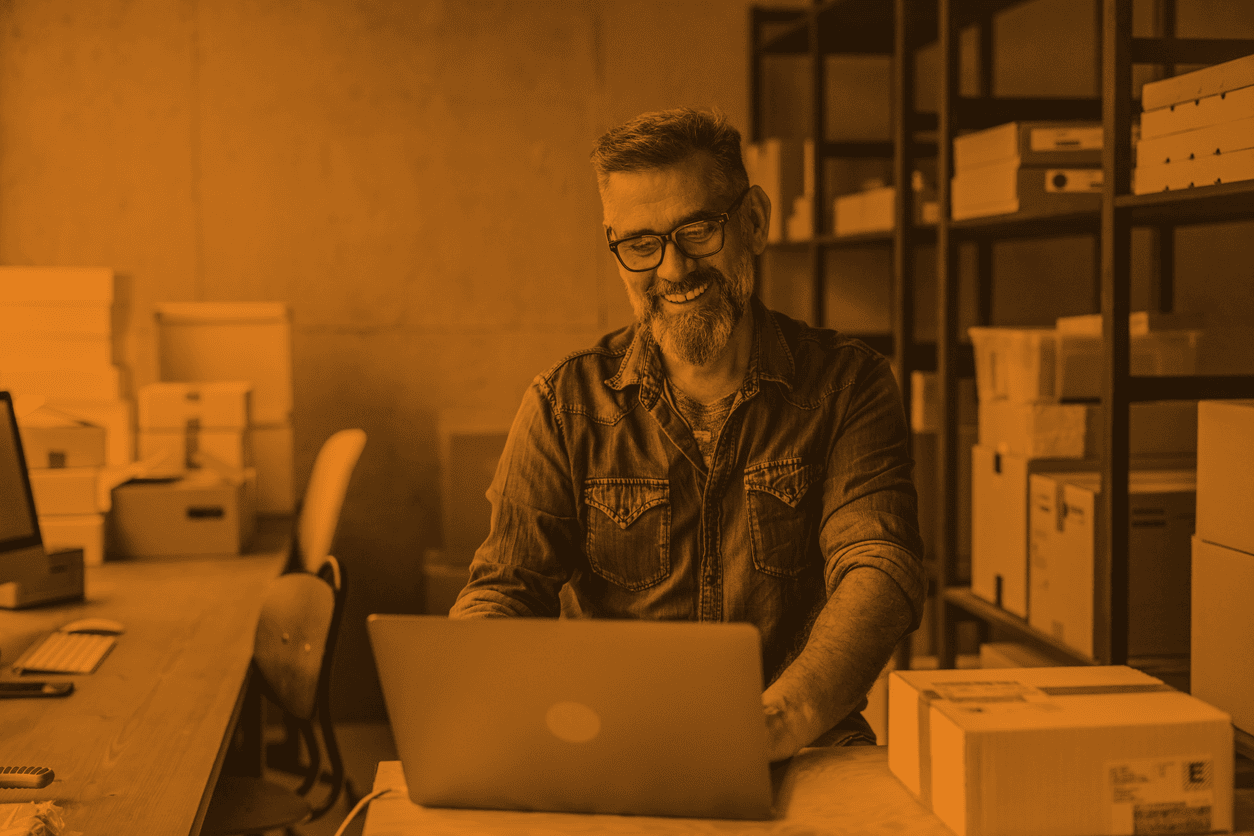
Most ERP systems operate on an infinite capacity scheduling system. Infinite is defined as “having no limits or boundaries in time.” Changes in your company’s production allows the schedule to fill in jobs to a limitless number of days, hours, and machine shifts. But the drawback of infinite capacity scheduling is that it’s too easy for managers to fool themselves into thinking jobs can be adjusted without inevitable consequences to budget and deadlines.
So, is infinite scheduling the right production management solution for a workplace with real-world constraints? Not always.
Finite scheduling defines time that is actually worked, taking limitations by different resources into consideration. By creating a realistic model of shift times, materials, number of operations, machine set up times and cycle times, this allows for a more accurate view of your shop floor’s capacity.
Production planning with finite scheduling anchors decisions in real-time data. Being able to view the shop floor with real-time restrictions gives managers the opportunity to see the tradeoffs in delivery dates, increased labor costs, expedited shipping costs and other variables when confronted with real-world time altering factors, such as rush jobs, downtimes, material outages, etc.
“What-if scenarios” can be evaluated in a framework of real-world constraints with production planning systems like JobPack®. With a drag-and-drop graphical user interface, a management team can evaluate capacity, costs, and delivery dates by creating different scenarios that automatically adjust the schedule to see what impact those actions have, and if those are not the desired outcomes, then the schedule can be instantly reverted back to the original.
Finite scheduling systems are particularly helpful for integrating various production schedules. For instance, if one department or process is on a two-shift schedule, and another department, such as shipping, is on a single shift, finite capacity scheduling provides accurate date projections that account for these real-world manufacturing variables.
When production scheduling data is constrained to finite scheduling, the result is improved accuracy and greater accountability in production planning scheduling. Better data will lead you to making better decisions. And better decisions on the production floor means greater satisfaction both internally and with external customers.