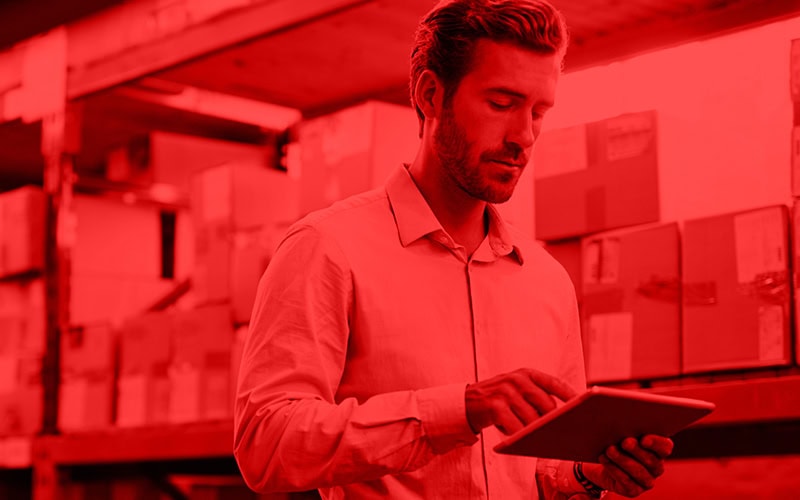
Your ERP system isn’t enough.
No production planning solution is complete if it doesn’t help a business reliably forecast their inventory needs. After all, it’s not just machine breakdowns or labor shortages that can bring a production shop to a halt. A lack of necessary materials can also hold up a project, which can have a domino effect on subsequent production timelines.
For decades, Material Requirements Planning (MRP) and its successor, Enterprise Resource Planning (ERP) have attempted to solve this problem by helping manufacturers predict their resource requirements. However, many of these solutions have come up short due to a lack of data, insufficient scheduling tools, or poor data representation (by which we mean bad user interfaces).
We designed JobPack® to resolve these pain points. As both stand-alone scheduling and machine monitoring software and a tool that can fully integrate with your ERP system, we can give you the production visibility you need to stay ahead of your resource planning. Here’s how.
1. Work with complete production data.
Many production shops are still working either off of spreadsheets, or systems that do not provide a complete overview of operations on the manufacturing floor. For instance, without machine monitoring, managers can’t know whether their production plan is still running according to the schedule they had laid out weeks prior.
JobPack®’s machine monitoring helps production shops gather more complete data about their factory’s real-time operations. (This can aid not only inventory management, but capital expenditure planning as well, so that you can know when to invest in new machines.)
We also provide reporting tools that help manufacturers see performance data by end-of-day, -month, and -year. These reports can help you identify the root cause of any production errors (including inventory management problems), and will show if your adjustments have had the impact you were hoping for.
2. Schedule production with accurate lead times.
When production plans fail, it’s often because some crucial step wasn’t appropriately accounted for. For instance, the scheduler didn’t realize that one of the suppliers only conducted drop-offs on Wednesdays, or neglected to account for inspection time, or expected a machine to accomplish the task faster than its actual operation speed.
Similarly, a production plan can neglect to account for a sub-assembly and all its related material requirements. When this happens, a manufacturer can find themselves waiting to move forward with production because they’re still manufacturing some of the pieces needed to complete the assembly.
JobPack®’s scheduling tools help production planners enter in all the necessary data so that a manufacturer can easily see how lead times adjust once all the variables are accounted for. If multiple assemblies are involved, the scheduler can set up dependencies so that moving a downstream component up the calendar will automatically readjust the lead times on all supporting components, allowing you to run “what-if” scenarios to see how these changes affect delivery dates.
3. Receive notifications of critical stock shortages.
When products run low, the faster you find out the better. JobPack® allows you to set triggers which will then send notifications to a number of specified places: to your screen, to shop monitors, or to designated email addresses.
For instance, if a rush order from a valued client comes in, you may have enough stock to handle that project but not enough for the projects that follow. JobPack® can help you spot this discrepancy and order in new materials so they arrive on time.
4. Avoid overstocking inventory.
Inventory storage is expensive. It isn’t just the physical space, either. Larger inventories are harder to track, organize, and access. Product is more likely to get lost, and operators can lose time trying to track down a supply that should be on the shelves but has somehow been misplaced. A leaner inventory reduces these expenses.
Another consequence of inventory overstock is that many of these items, such as polyester resins, expanding polyurethane foams, paints, adhesives, rubbers, and other chemical agents have a limited shelf life. Moisture creeps in, materials oxidize, compounds grow unstable, and temperatures fluctuate, which can all contribute to spoiling a product. Once these items pass their expiration date, they must be thrown out. This waste is a financial loss to your company, and often has negative environmental consequences as well.
With accurate production forecasting and stock notifications in place, manufacturers can place their orders more efficiently and with greater confidence.
5. Understand your true capacity at a glance.
Finally, manufacturers shouldn’t overlook the value of an intuitive user interface. People make mistakes, especially when trying to track hundreds of variables at a time. Good software supports users by removing opportunities for error and making it easier to see how scheduling decisions will impact their inventory requirements.
For instance, if you’re considering running some overtime in an attempt to bring some of your projects in on time, JobPack® can help you visualize if this will also bring forward the timeline on your inventory requirements. All the overtime in the world won’t help you if you don’t have the raw materials to keep production running.
JobPack® removes the unknown elements from material requirements planning.
With so many moving pieces in play, manufacturers can’t afford to be in the dark when it comes to their resource management. Not knowing is a liability. By increasing your visibility into your manufacturing operations, JobPack® makes that liability a thing of the past. Contact us today for a demo of our product.