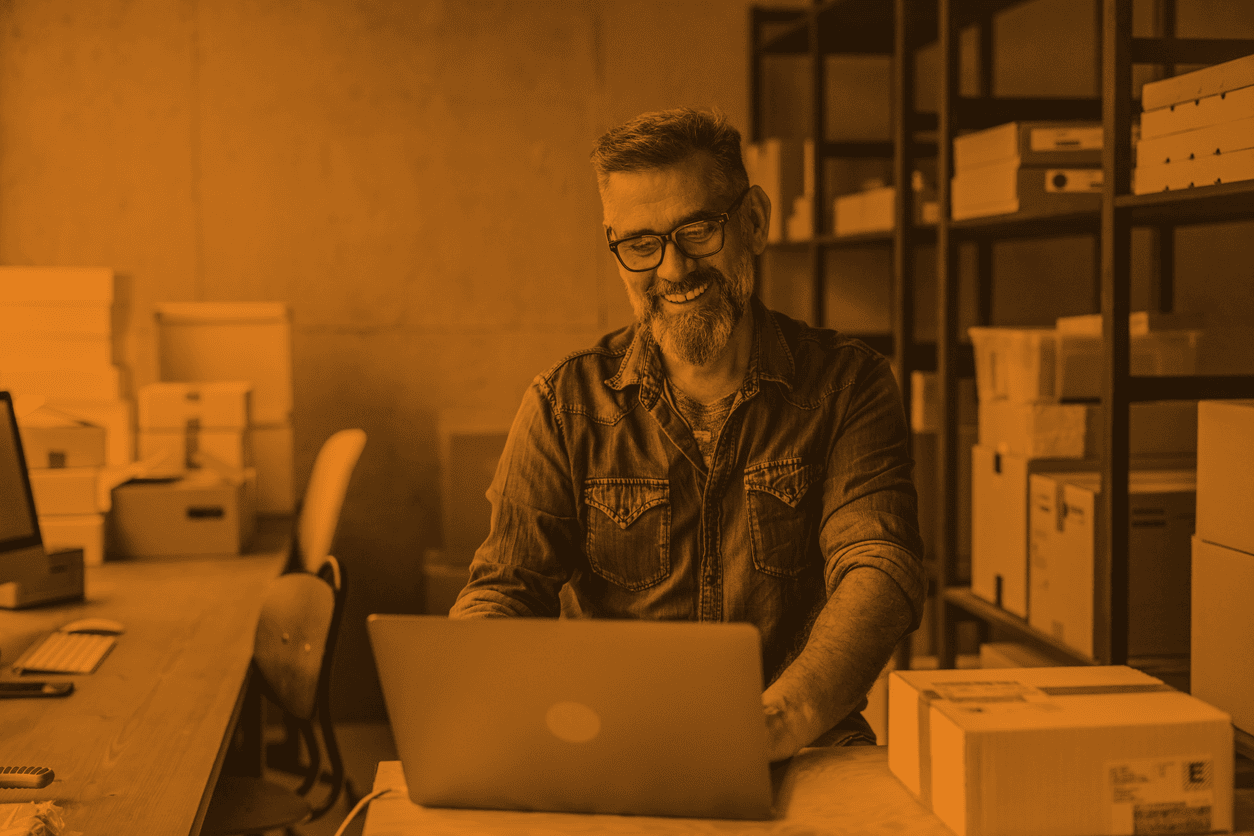
Conflicts between employees at all levels create a toxic work environment. Better scheduling software can nip the blame game in the bud.
Imagine the following scenario: The owner of a production shop receives a last-minute work order from a valued client. The owner accepts this job hoping to impress the client with a timely turn-around. Instead, the project comes in late, and the client is unhappy.
The owner asks the production manager what went wrong. The production manager notices that it took longer to finish several of the production steps than it should have given his standard lead time references and goes to the scheduler to find out what happened. The scheduler is frustrated because their production plan got thrown into disarray by the last-minute change, but goes to talk to the machine operator about the delay. The operator is upset because they feel like everyone is breathing down their neck. No one is exactly sure where the problem arose, but everyone thinks it’s someone else’s fault.
This kind of scenario is surprisingly common, but the issue may have less to do with people and more to do with software. When no one has any insight into why things are going wrong, it erodes trust in the team and causes blame to be cast without any evidence to back it up. Visibility into the production schedule shows owners and managers the underlying causes of many production problems. It gives schedulers the data to plan more effectively, and it helps operators account for their time.
Here’s how the visibility granted by production scheduling software can benefit all levels of your company and prevent mistrust from growing into an HR crisis.
For owners: Gain a better perspective on your team’s work capacity.
Every owner wants to make decisions with full confidence in their team’s ability to carry through. When the team falters, the inevitable question is: Was my confidence misplaced, or did I make a poor decision?
Without visibility into your production processes, the answer may never be obvious—especially as it probably varies on a case-by-case basis. But when they do have access to that insight, owners gain a better perspective into their own operations, allowing them to provide better estimates to their clients, and accept work with a better understanding of how it will impact their team.
For managers: Avoid developing a culture of mistrust.
Production managers are often in a difficult middle position: they’re in charge of making sure everything is running smoothly, even when the owner throws them a curveball. And when anything goes sideways, they’re the ones who have to do the investigation to find out why. Trying to conduct any review is likely to raise hackles, especially if the manager struggles to get to the root cause.
Production planning software not only makes those root causes more identifiable—it can also head off any awkward encounters by placing the answers that the manager needs right within reach.
For schedulers: Defend your production schedule with data.
The pressure to make everything work often falls most squarely on the shoulders of the production scheduler. Schedulers can sometimes find themselves in a frustrating situation: the better they are at jigsaw piecing a production plan together, the more pieces they’re given to cram into the puzzle.
Sometimes, the expectations are beyond what a scheduler can reasonably execute, even with the most optimistic planning. And, of course, optimistic plans that have little likelihood of success aren’t how most manufacturing shops want to operate.
As the scheduler is working most directly with the scheduling software, they’ll be the ones most affected by an upgrade. To start, they’ll be able to begin accounting for so many of the little things that never seemed to pull together before. But they’ll also have a powerful tool to point to whenever someone comes asking for the impossible. Owners and managers can even ask them to create “what if” scenarios showing what kind of consequences a decision will have on the production schedule so that they can judge whether a plan is feasible before taking on work.
For operators: Show your work.
We’re aware that the operators on your shop floor aren’t the ones driving scheduling software decisions, but any kind of monitoring product can create mistrust among workers, especially if they think it’s questioning their integrity. In the manufacturing world, however, machine monitoring can offer operators a form of support.
Operators aren’t in control of everything happening on the shop floor. If they run out of a part and need to head back to the warehouse to gather more inventory, it will slow down their output. If they have to wait for an inspector to come around, it will mean idle time on the machine. When these delays aren’t recorded, and someone asks them a week later why they took so long to do their job last Thursday, it is unlikely they’ll remember exactly why.
Machine monitoring software, combined with more detailed production planning, acts like a receipt in this scenario. Best of all, because the data is centrally located, operators won’t even need to explain themselves. Anyone with access to the software will have their explanation from the data itself.
If your production isn’t running to plan, the true culprit may be your scheduling software.
Manufacturing is a complex industry, with many unknown variables. Keeping everyone on the same page can prevent misunderstandings from spiraling, but that’s a heavy lift if your scheduling software isn’t up to the challenge.
At JobPack®, our software offers real-time insight into operations at the shop floor level, and helps you plan jobs more accurately. We take the mystery out of production scheduling so that your team can have the visibility necessary to make decisions, diagnose mistakes, and move forward with clarity. Contact us today if you would like to set up a demo.