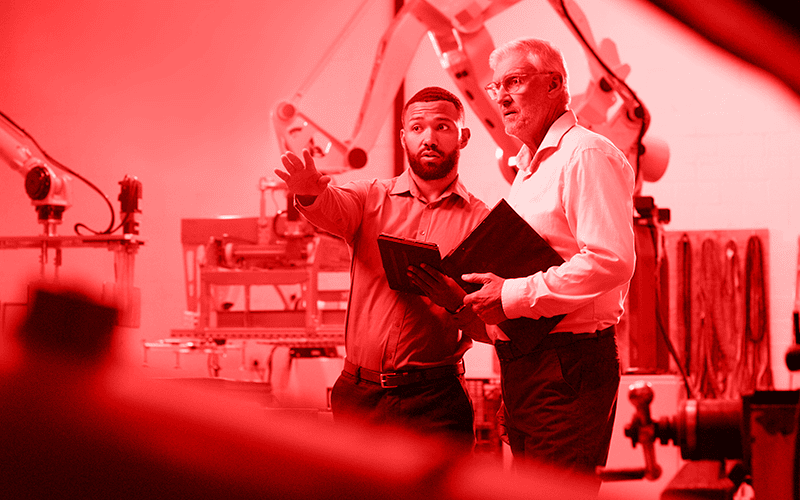
How Machine Monitoring Aids Overall Equipment Effectiveness
Machine monitoring gives manufacturers the inside look at how their factory is really performing.
In a competitive industry such as manufacturing, businesses succeed or fail on their ability to manage their operations efficiently. And when it comes to the factory floor, a lot of efficiency is gained or lost based on equipment performance. Overall Equipment Effectiveness (OEE) is how businesses measure that performance, but attaining that measurement is no simple task.
At its most basic, OEE is a measurement of machine availability, performance, and quality:
- Availability: What is the planned availability of a machine, and how much was it actually available for use? For instance, if a factory runs in 8-hour shifts, then the machine has a planned availability of 8 hours. But if it undergoes scheduled maintenance during the last two hours of a shift, then its actual availability was 6 hours.
- Performance: How many parts were booked for a shift, and how many were actually produced? A scheduler might expect a machine to produce 8 parts in a shift based on standard run times, but if the actual number of parts produced was 6, then that represents a loss in performance.
- Quality: If a machine produces 6 parts in a shift, but two of them are rejected because they are nonconforming, then the actual output was four parts.
Take these numbers together, and it’s clear to see how a manufacturer who is expecting a machine to be running at full strength all day according to the standard run time and with no part defects might quickly run into difficulties when the messy reality of shop floor operations sets in. At the same time, a manufacturer who understands that few things ever run to plan may still believe those numbers could be improved. The question is determining where the problems lie, and what can be done to improve the situation. That’s where machine monitoring steps in.
Here are six ways machine monitoring helps improve OEE.
1. Measure downtime and identify root causes.
Machines experience downtime for a number of reasons. Sometimes, a machine is down because a part has broken and it needs repairs, but more often the reasons are more mundane: routine maintenance, regular cleaning, the operator has to wait for an inspection, new stock has to be brought in from the warehouse—the list goes on. These reasons can be hard to track, and if there is no record of the down time or why it happened, it can lead to suspicion of the shop floor operators.
Machine monitoring not only shows where the downtime is, it also tracks why it happened. Using JobPack®’s machine monitoring module, operators can even create custom codes to specify what the downtime cause was, so that over time production managers can build a more comprehensive picture of the workflow on the factory floor—and identify ways to streamline it.
2. Schedule downtime more effectively.
As we mentioned, some downtime is necessary. But how you schedule it can make a big difference in how your factory operates. If Machine A is waiting on parts from Machine B, but Machine B is offline for a couple hours due to non-critical maintenance, it can throw off not only Machine A, but any other processes downstream of that delay. By helping operators, schedulers, and managers communicate more effectively, machine monitoring can reduce inefficient downtime scheduling and keep the factory floor running smoothly.
3. Build a history of machine use for analysis.
By the time many manufacturers notice something’s not working well, the opportunity to collect data about why is lost. In order to examine past data, manufacturers need to be collecting that data in the first place. Machine monitoring builds that record so that the information manufacturers need is prepared before they need it.
4. Compare planned vs. actual KPIs for more accurate production times.
When activity on the shop floor doesn’t line up with the production plan, manufacturers have two options. They can try to find a way to align operations with the plan, or they can adjust their standard lead time to better match real-life conditions. Machine monitoring helps manufacturers identify where shop performance can be improved, and when the lead time has to give.
5. Home in on lagging resources and analyze costs for replacement or investment.
Equipment doesn’t last forever. It wears down, newer technologies enter the market, old models are no longer maintained. Machine monitoring draws attention to which resources are falling behind. Once you identify a machine that’s not hitting the right KPIs, you can create a replacement schedule.
Alternatively, if you notice a consistent bottleneck at one machine, you can review your machine monitoring data to determine if it’s performing to speed. If the machine is working well, that may be a sign you need to invest in a second machine to handle the workload.
6. Monitor the live status of operations and set alerts for downtimes.
Finally, machine monitoring means managers don’t have to be on the factory floor to check the status of jobs and projects. Our JobPack® module equips managers with a dashboard that shows what machines are running, which projects they’re working on, and whether they’re running on time. Managers can even configure their system to send alerts for different conditions.
Machine monitoring gives you the data you need to make the best decisions for your organization.
You don’t have to run your factory without answers. The insights provided by machine monitoring software can improve communications with your team, clarify which areas of your shop floor need more support, and give you a performance history that you can use to track KPIs and improvements over time.