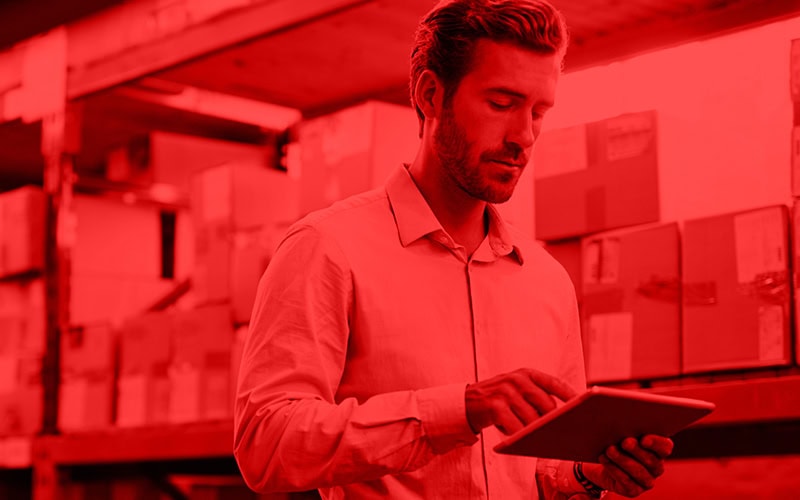
How Our Production Scheduler Brings Order to Your Shop Floor
Tame the chaos with a production scheduler that targets core manufacturing challenges.
The only constant on a shop floor is change. Deadlines shift, supplies arrive early or late, machines go down or come back online, and because the production process is so interconnected, each shift causes a cascade of further changes. It’s a lot to keep track of—and yet, managing all the variables on a shop floor is crucial. Without the agility to adapt to changing circumstances, manufacturers risk missing out on jobs that could give them an edge on the competition, or prove to be important stepping stones to building their business.
The sheer amount of activity on a shop floor, however, has outgrown traditional scheduling methods. Schedulers who are still reliant on whiteboards or paper packets regularly face inaccurate job information, missing paperwork, and supply chain disruptions, resulting in unplanned downtime, jobs delivered late, and disappointed clients. The pace—and expectations—of the industry has increased, and to match the demands of the marketplace, manufacturers need a tool that does more than just keep up.
JobPack is built to address the biggest production scheduling hurdles on today’s shop floors by consolidating an avalanche of data and variables into an accessible, adaptable format. With JobPack, you have the visibility you need to make critical business decisions—including being able to view the potential impacts of your choices. When shop floors verge on chaos, JobPack helps you find the signal in the noise so that you can keep your factory on track. Here’s how.
1. Achieve real-time visibility into your capacity and job status.
The first, and maybe most important, step in wrangling your production process is simply understanding it. While spreadsheets and whiteboards can give you an idea of the flow of materials through the production process, JobPack takes transparency to a whole new level with machine monitoring capabilities that offer real-time, granular data.
When time is a factor, your decisions are only as good as the information you have. JobPack’s level of detailed visibility lets you respond to requests and changes swiftly and authoritatively. Answer client questions about job status on the spot, or gauge your capacity to accept an entirely new job. If a machine goes out of service, begin adapting your production schedule immediately to avoid major delays. And with historical shop floor data, you can quickly catch slowdowns and bottlenecks, and either plan for maintenance or optimize your production workflows.
2. Absorb—and even capitalize on—variability.
There’s a bottleneck in the supply chain, and materials you need for one job will be arriving late. This disruption pushes the start date for the job back, and now it’s unlikely you’ll be able to deliver it on time. With JobPack, you can see exactly what the impact will be—but you can also run out other possibilities to make up the loss.
Could you slot a different job into the production process and deliver it early? What if you accepted a new job that you’d otherwise be unable to accommodate? How would that impact your shift schedules, or the other jobs already in progress? JobPack’s what-if planning capabilities give you all the possibilities at your fingertips, and a low-stakes, low-commitment sandbox in which to gauge the results. Use your shop data to craft the optimum plan in response to unexpected changes—and you might even come out ahead.
3. Ditch the clutter of manual scheduling and paper packets.
Any system that relies on manual updates is at constant risk of errors. Busy workers may forget to update job details or enter information incorrectly, and the possibility of errors increases exponentially the more manual systems are in play. In addition, whiteboards and paper packets take up valuable space and can get lost or damaged, meaning job success hinges on a single point of failure.
Given the complexity of a shop floor, manufacturers need a single source of truth for job data and updates. On top of that, whatever system you use needs to be readily accessible to operators, schedulers, account managers, and anyone else who might need the latest information. JobPack centralizes job details and status updates in a format that’s readable at a glance, and is available in a web interface on computers and mobile devices, keeping critical data safe from loss or corruption while making it easy to look up and share.
4. Plan your maintenance—don’t let your equipment plan it for you.
Unplanned downtime costs industrial manufacturers as a whole as much as $50 billion per year. If your shop is operating on a run-to-fail strategy, you have no control over when the downtime strikes—your equipment will fail when it fails, even if you’re in the middle of a high-priority job with a tight turnaround.
Instead, leverage the transparency that JobPack offers to monitor your machines’ performance and pinpoint when they begin to show signs of wear. Then, you can use historical production data and what-if planning to choose a maintenance window that disrupts your operations as little as possible.
5. Boost on-time delivery rates.
Most customers want an idea of how long a job will take. Without detailed data on your own shop’s production rates, it’s tempting to turn to standard lead times for an estimate. But these quotes don’t take into account your shop floor’s capacity, your supply chain, your workforce, the special requirements of the job, or dozens of other factors that might affect the turnaround time. Standard lead times limit how precisely you can set expectations with your customers—and vague expectations leave the door open for disappointment.
The real-time capacity monitoring and granular performance data in JobPack help you generate an estimate based on the concrete realities of the job and your shop. With details from JobPack, you can offer an informed timeline with the confidence that your shop can deliver on it. Your customers are impressed and satisfied, and you minimize the financial penalties of missed deadlines.
Stay nimble in the face of uncertainty with JobPack.
The manufacturing industry will always have its share of surprises, emergencies, and other unknowns ready to upend your carefully planned production schedule. Manual scheduling processes are too sluggish and brittle to adapt with the speed that Industry 4.0 demands, and as a result, efficiency and on-time delivery rates suffer. JobPack gives your business the tools to predict what you can, and pivot when you can’t.
To learn more about how JobPack can help you streamline your production processes and rein in the chaos, request a demo today.