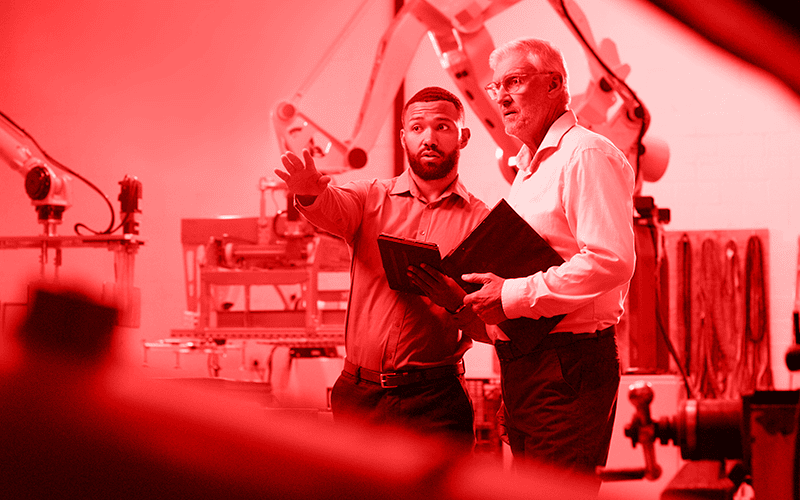
Why Machine Monitoring Is the Missing Link in Your Production Scheduling
Optimize your production schedule with minute-by-minute machine data.
Do you know what your machines are doing right now?
Spreadsheets and whiteboards can tell manufacturers what the equipment on their shop floors should be doing at any given moment. But there’s plenty of room for chaos in the gap between what should be and what is. Unplanned downtime, production errors, and supply shortages can all disrupt a tightly packed production schedule—and the longer they go undetected, the more the delays compound.
Agility is one of a manufacturer’s greatest assets, and machine monitoring provides you with real-time operational visibility that allows you to flag issues at a glance and adapt your production schedule on the fly. With detailed productivity and quality information, you can identify potential equipment issues before they become catastrophic. And with robust analytics, you can leverage your production data into a tool for finding operational efficiencies that stack into a significant competitive advantage.
Here are four key ways that machine monitoring enhances your production scheduling and keeps you ahead of the pack.
Identify system changes and respond in real time.
For manufacturers, the ability to accurately estimate lead times on a project is essential. The turnaround time on a job can be the deciding factor in whether a client decides to order from you—or whether you choose to accept the order. Lead times are the building blocks of your production schedule, and the margins are often fine: leaving too much of your equipment idle is a wasted opportunity, but double-booking your machinery is a recipe for delays.
To maximize their productivity, manufacturers need a precise understanding of their shop’s operational efficiency. An estimated lead time hinges on accurately predicting how long it will take your shop to turn out a set quantity of products—but if your output rate changes abruptly and you don’t catch it, you could be left with a scheduling headache and costly fees.
Machine monitoring gives you real-time insight into the overall equipment effectiveness of your shop floor. If a machine slows down, begins turning out flawed products, or fails completely, a machine monitoring system can alert you immediately so that you can adapt your production schedule. Machine monitoring data can also reveal decreased efficiency from non-equipment-related causes, like a materials shortage or an operator issue. Spotting these kinds of slowdowns early gives you time to organize a workaround before you’re faced with unrecoverable delays and a disappointed customer.
Refine production processes for greater efficiency.
Continuous improvement is key to staying ahead of competing manufacturers in a demanding industry. Even the most marginal efficiency gains add up over time, but in order to find hidden opportunities, manufacturers need as much visibility as possible into their processes.
With machine monitoring, you can track the status and activity of your equipment in fine-grained detail, giving you the opportunity to identify and improve on even minor disruptions. If a 3d printer sends a supply alert at 20% print medium remaining, for example, but consistently runs out of materials before replenishment and has to pause, detailed machine monitoring data can help you identify and eliminate the delay. Even if it only wins you back a few minutes per cycle, every little bit counts.
Anticipate maintenance needs and plan the ideal window.
Equipment wear is inevitable, and even in the most modern factories, the old truism still stands: if you don’t schedule maintenance, your equipment will schedule it for you. An unexpected equipment failure can throw a wrench into carefully planned production schedules, causing bottlenecks and delays and ratcheting up costs. In addition, failures are often more expensive to repair and result in longer downtimes than regular preventive maintenance.
Equipment will always need to be maintained, but it’s possible to plan ahead and schedule the downtime for when it will have the least impact on your shop floor operations. Machine monitoring allows you to keep a close eye on the performance of your equipment and identify when wear is starting to show—or when it’s simply due for regular tune-ups. Then you can review your monitoring data for a window of availability, and slot your maintenance in when it’s most convenient (or, at a minimum, least disruptive).
Harness production data to inform business decisions.
As powerful as machine monitoring can be in the moment, it becomes even more valuable when monitoring data is collected over time. Historical data gives manufacturers a detailed, 360-degree view of their operations as they evolve, and offers the opportunity to identify patterns, follow trends, and measure return on investment.
Longitudinal equipment data enhances every machine monitoring advantage we’ve covered so far. With it, you can develop informed predictions about turnaround times, process changes, and equipment life cycles. Leverage these predictions to make educated business decisions, and then monitor the outcome to improve your models further.
Integrate your machine monitoring solution with a fully fledged ERP, and you can gain even deeper insights by cross-referencing production data with broader business variables. Both systems working together can help you discover how a marketing push interacts with your production schedule, or production schedule changes impact consumables ordering. Machine monitoring provides the next crucial piece in a holistic, data-driven view of your business.
Achieve flexible and lightweight machine monitoring at any scale with JobPack.
Our production scheduler is ready to dive as deep as you like into your production data. That said, gaining the visibility you need into your shop floor activity doesn’t have to be a heavy lift. JobPack integrates with existing ERP and CNC systems, but also functions as a standalone production scheduler, adding insight to your operations without adding a burdensome technology implementation to your plate. To learn more about how JobPack can bring clarity to your shop floor, contact us today.